Advantages
- Bright surface
- No decarburization
- No oxidation
- Minimized distortion
- Reproducibility
- Vacuum high
temperature brazing
- Economical
|
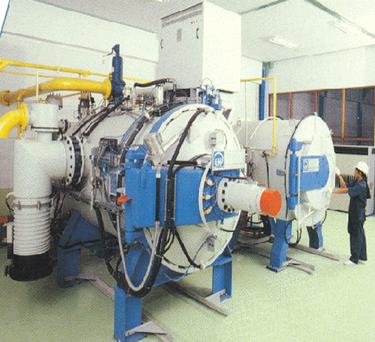 |
TECHNICAL
DATA VKNQ |
Working Space
600x600x900 mm
- Charge Weight
500 Kgs max
- Rated Temp.
1,300 oC max
- Temp. Uniformity
< + - 5 oK
- Quenching N2
Gas 6~10 bars
- Vacuum 10 -2
~10 -5 mbars
Manufactured by ALD (Germany)
|
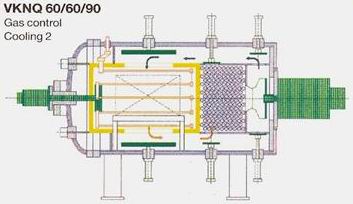 |
PROCESS
CONVECTIVE HEATING |
- Heat transfer
takes place by radiation only in vacuum, which is
ineffective at lower than 500 oC and develop large
temperature difference between surface and core of
work piece. Such temperature difference should make
thermal stress, which might cause some distortion
of work piece.
- By adding N2
gas of 2 bars for heat convector, homogeneous and
rapid heating can be achieved.
|
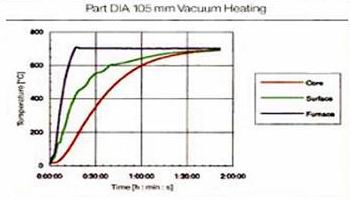
|
PROCESS
MARQUENCHING |
- In case of
parts with large sections and complicated shapes,
rapid quenching may lead to crack and/or serious distortion
on work piece.
- By programmed
controlling quenching above Ms point of material by
using two thermocouples installed on surface and core
of a dummy with charge, minimized distortion can be
achieved.
|
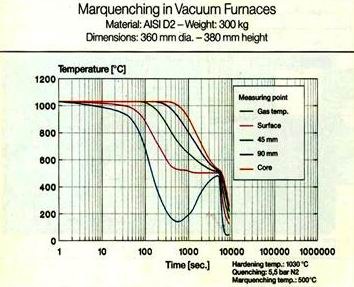 |
PROCESS
Reversible Direction |
QUENCHING
- In quenching
process, it is said that steel has to be quenched
as fast and slowly as possible.
- The former
is for enough cooling speed to obtain ideal micro
structure, the latter is for prevent cracking and
severe distortion of work.
- Our furnace
makes both available by high pressure gas quenching,
by programmable reversible cooling and by Marquenching
|
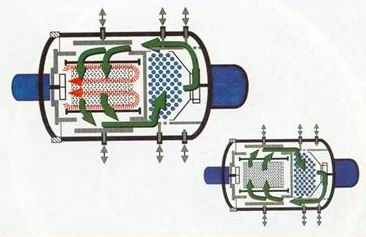 |
Concept
Heat Treatment of HIGH ALLOYED TOOL STEELS |
- Hardening of
high alloyed tool steels have to be carried out in
way of vacuum process, in order to prevent any oxidation
and decarburization.
- In our vacuum
process, a dummy block of which diameter is equivalent
to the control section of work piece to be hardened.
Two thermocouples installed at both core and surface
of the dummy can manage the temperature control of
work piece at both surface and core throughout its
hardening procedure. By this way we are able to ;
-
- manage any
thermal stress which may arise while heating work
piece up and minimize any distortion.
- prevent insufficient
austenitizing of core and over solution of carbides
through austenitizing by controling austenitizing
by core temperature.
- apply marquenching
procedure in order to prevent cracking and minimize
any distortion by both thermal and transforming stress
in case of complicated shape work piece.
Three high temperature temperings are to done as general
rule. The first temper is for decomposing retained
austenite which is unavoidable in high carbon and
high-alloyed tool steels. By the second tempering
we control hardness required. The third tempering
is stress relieving to prevent any cracking and deforming
through the subsequent process.
|
Hot
work Alloyed Tool Steel |
- Though hot
work alloyed tool steels have good hardenability and
be enable to harden by gas quenching in vacuum process,
as the size of mold become larger recently, early
cracking problem has reported and quenching speed
has been to be discussed.
- According to
CCT curve left, bainite transforms in earlier stage
than pearlite and it will accompany some amount of
retained austenite in matrix. Carbides precipitated
on boundary of austenite by tempering are considered
the cause of early cracking.
- In our vacuum
process, quenching nitrogen up to 10 bars can be used
and can increase effective quenching speed by alternative
direction quench program. Thus we will try to reduce
bainite, intending long life mold making.
- We also recommend
the late bainite transform type steels recently announced.
|
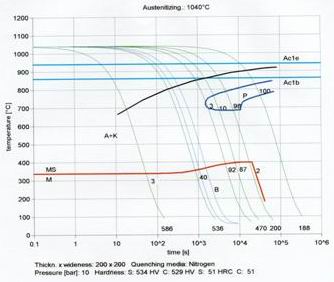 |
Cold
Work Alloyed Tool Steels |
- Retained austenite
may not be avoided by quenching this kind of steels
because of high carbon and alloyed elements.
- Retained austenite
often causes cracking or distortion of work piece
in subsequent wire cut or grinding, subzero treatment
or 2 times high temperature tempering are recommendable.
- By high temperature
tempering, hardness specified shall be HRC55~58. When
HRC60 is needed, austenitizing temperature must be
applied 1070oC that is higher than usual one of 1030oC,
in order to harden by second hardening. This process
is not recommendable because it increases retained
austenite.
- Further stress
relieving is to be carried out for any subsequent
machining process
|
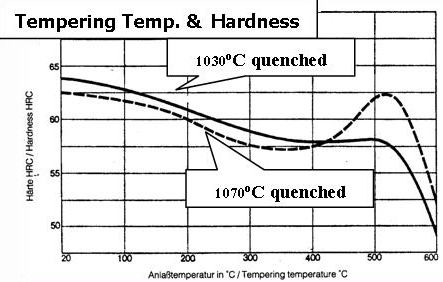 |
High
Speed Steels |
- High speed steel,
as it shown in its name, has developed for cutting
tools which can keep high hardness even if temperature
of tools come up into red condition by high speed
cutting. For this purpose, austenitizing must be carried
out at 1200oC for high hardness.
- Tempering shall
be carried out more than 3 times, as this steel has
a lot of retained austenite after quenched.
- Thin cutting
tools can be straightened taking an advantage of existing
retained austenite after quenched while warm.
- High speed steel
may be used in room temperature and instead high toughness
is required. In this case, austenitizing shall be
lower than usual. The pocess for high toughness is
called as under hardening.
|
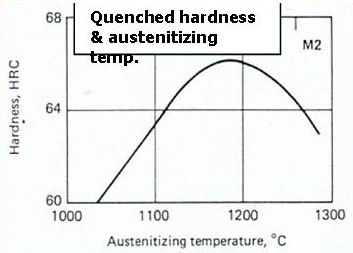
|
Vacuum
high temperatureAdvantageous BRAZING |
- Oxide film
on base metal bursts and be removed by vacuum and
metal wall gets wet with alloy which enables good
brazing.
- By heating
the work piece to high temperature in vacuum, enough
diffusion is available between metals and good bonding
with no inclusion nor gas hole can be attained.
- Very narrow
brazing gaps of less than 0.05mm makes bonding metals
with high strength and good accuracy.
|
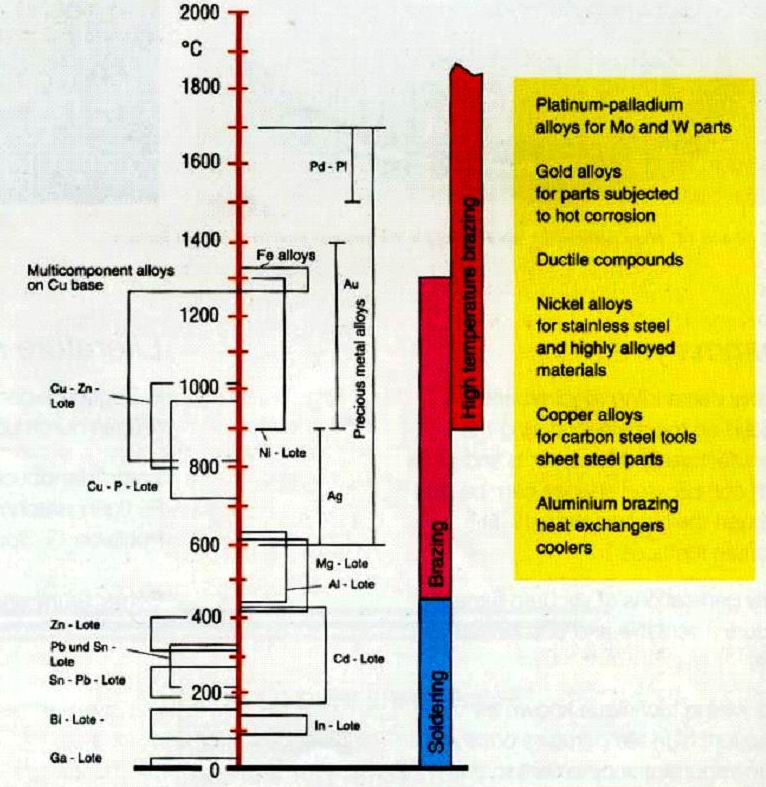 |
|
Top
|