|
|
|
FLAME
HARDENING
|
|
|
- Flame hardening
is one of surface hardening process, in which a thin
surface shell of steel or cast iron is heated rapidly
to Austenite by high temperature flame of mix gas
of propane and oxygen, then quickly be quenched to
get high hardness.
- The process
has advantages to improve abrasion resistance and
fatigue limit by compressive residual stress created
by surface hardening as same as induction hardening.
- The process
has no limit of part size and/or weight, and is suitable
and economical for small scale production. The cost
for making induction coil can be neglected.
|
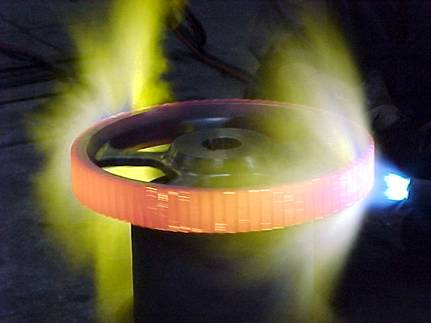 |
- Flame for hardening
shall be neutral. By mix ratio of propane and oxygen
of 1.4 must be used for the highest temperature of
2,930oC obtainable.
- Flame hardening
is applicable on any heattreatable steel and cast
iron.
- The higher austenitizing
temperature by 20~30oC is suitable.
- The preheating
is recommendable in order to avoid rapid heating and
cooling on such work piece as of intricate shape or
of gray cast iron which has apprehension of cracking.
- By preheating
the hardened depth can be deeper and also cracking
season cracking can be prevented by self tempering
effect.
- Hardness obtainable
by this process on cast iron depend on its amount
of pearlite in matrix. Pre-normalizing for increasing
matrix pearlite is recommendable for the purpose.
|
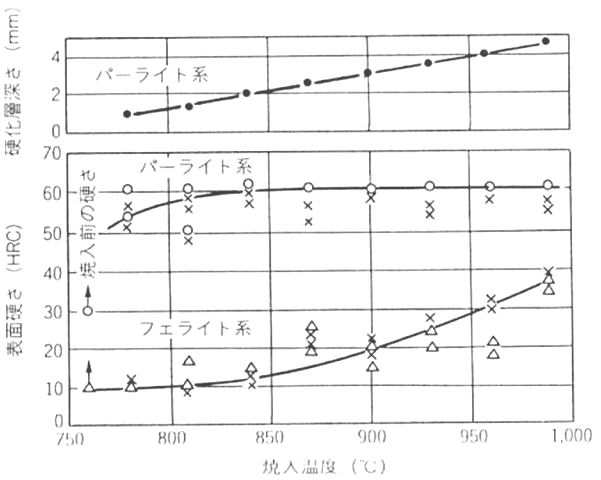 |
Effects
of matrix of FCD on flame hardened hardness and depth.
|
Response
of steel and cast to flame hardening (HRC)
|
Material
|
JIS
Symbol
|
Air
Cool
|
Oil
Cool
|
Water
Cool
|
SC
|
S20C,
S35C
|
-
|
-
|
33
~ 50
|
S38C,
S50C
|
-
|
52
~ 58
|
55
~ 60
|
S53C,
S58C
|
50
~ 60
|
58
~ 62
|
60
~ 63
|
SM
|
SCM
435
|
-
|
50
~ 55
|
50
~ 60
|
SCM
440
|
52
~ 56
|
52
~ 56
|
55
~60
|
SK-
|
SK
3, 4, 5, 6
|
52
~ 56
|
58
~ 62
|
62
~ 65
|
SUJ
|
SUJ
2
|
55
~ 56
|
55
~ 60
|
62
~ 64
|
FC
|
FC
300
|
-
|
43
~ 48
|
43
~ 48
|
FC
350
|
-
|
48
~ 52
|
48
~ 52
|
FCD
|
FCD
600
|
-
|
-
|
35
~ 45
|
FCD
700
|
-
|
52
~ 56
|
55
~ 60
|
|
|
|
|